... Dr. Florian Haakmann from thyssenkrupp AG
Interview from 19.7.2023
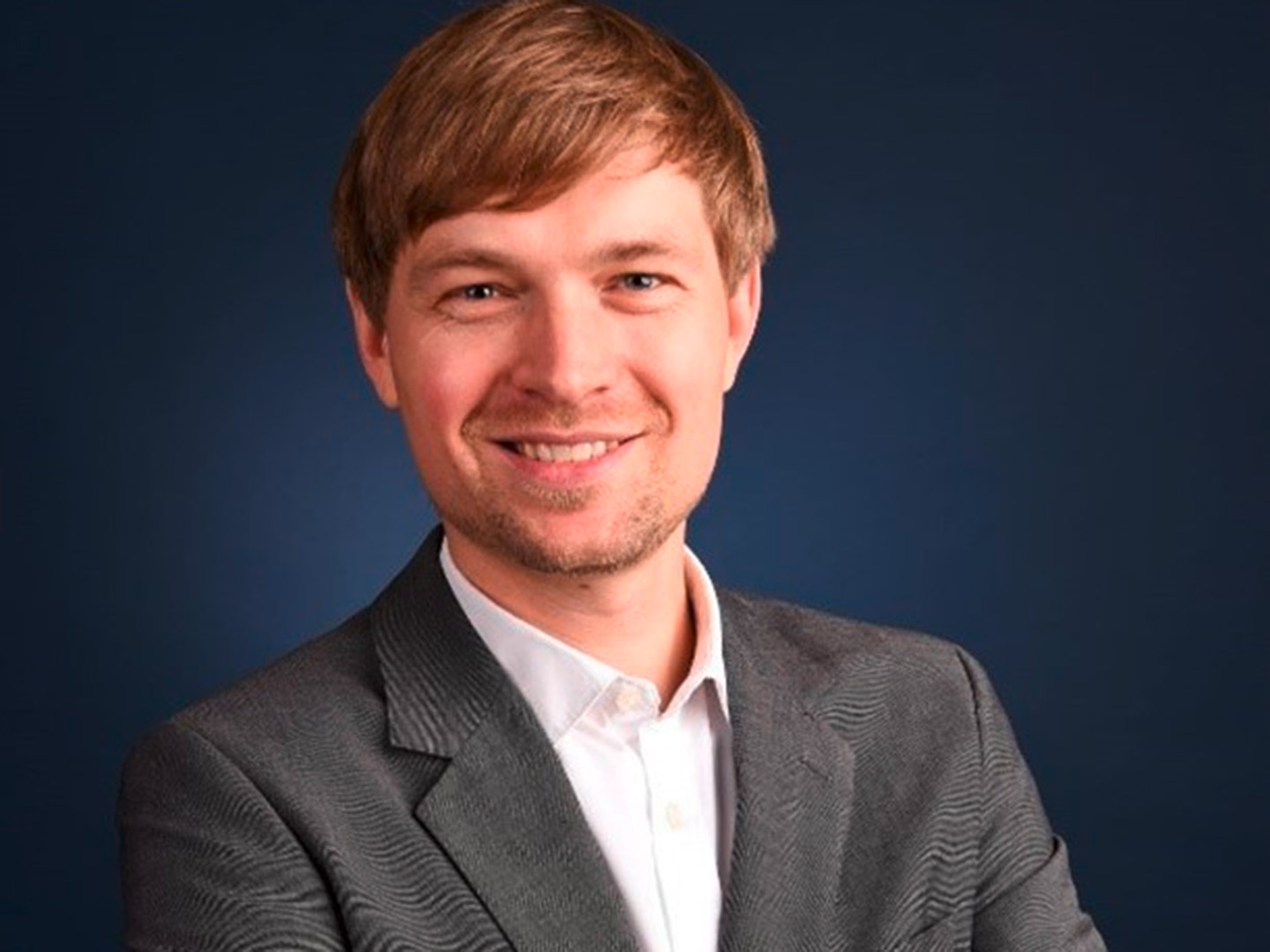
As subproject leader of L-0, what has been achieved so far in the Carbon2Chem® joint project from your perspective?
Florian Haakmann: Europe, Germany and the steel industry have set themselves ambitious climate targets: climate neutrality by 2050 at the latest. To implement these targets and achieve climate neutrality, the use of carbon from point sources to replace fossil sources plays a decisive role. In particular, metallurgical gases from steel production with high CO2 and CO contents compared with the atmosphere are a particularly promising way of saving and recycling large quantities of CO2 quickly and in an energy-saving way. In the unique Carbon2Chem® collaborative network, consisting of academic and industrial partners, the technical feasibility and robustness of the process, in which basic chemicals such as methanol and urea are produced from metallurgical gases, were demonstrated in the pilot plant in Duisburg and in the laboratory at the Oberhausen site during the first phase of the project and in the second phase, which will run until May 2024. In parallel, different process concepts for technical implementation were drawn up and evaluated and compared with regard to the economic, techno-economic and ecological influencing factors.
What have been the highlights?
Florian Haakmann: One highlight is definitely the way of working together; the interdisciplinary and international project team creates an atmosphere that gives room for innovation, inspires a spirit of research and at the same time is determined to find solutions. Other highlights include the commissioning of the first scale-up methanol plant, which is already producing 60L of methanol per day, and the expansion of the project to evaluate possible plant locations and the use of additional CO2 sources in the course of the Carbon2Chem® upgrade.
What were the biggest challenges?
Florian Haakmann: The greatest challenge was and still is to explain the value of carbon capture and utilization (CCU) to society in an understandable way and to clarify the distinction from carbon capture and storage (CCS) processes. The confusion of terms and processes shows that there is still a lot of work to be done here, including at the level of the legal framework. What is clear, however, is that a carbon cycle economy without CCU is difficult to imagine and that this technology needs to be promoted from all sides in order to be able to replace fossil raw materials in the long term.
What are the next steps?
Florian Haakmann: The overriding goal is still to bring the technology into use in the large-scale plant. However, the environment in which we operate has also evolved and with the gradual replacement of coal by hydrogen as a reducing agent in the steel industry, the amount of CO2 and CO in the metallurgical gases is also expected to decrease, which requires a kind of "transformation plant" to be designed. In parallel, the focus of the project is on other CO2 sources and their utilization in addition to the C sources from the steel industry. To this end, we are interested in involving new partners and industries in order to further enable the CCU technology and bring it into large-scale use.