… Prof. Frank Atzler from Dresden Technical University
Interview of 25.01.2023
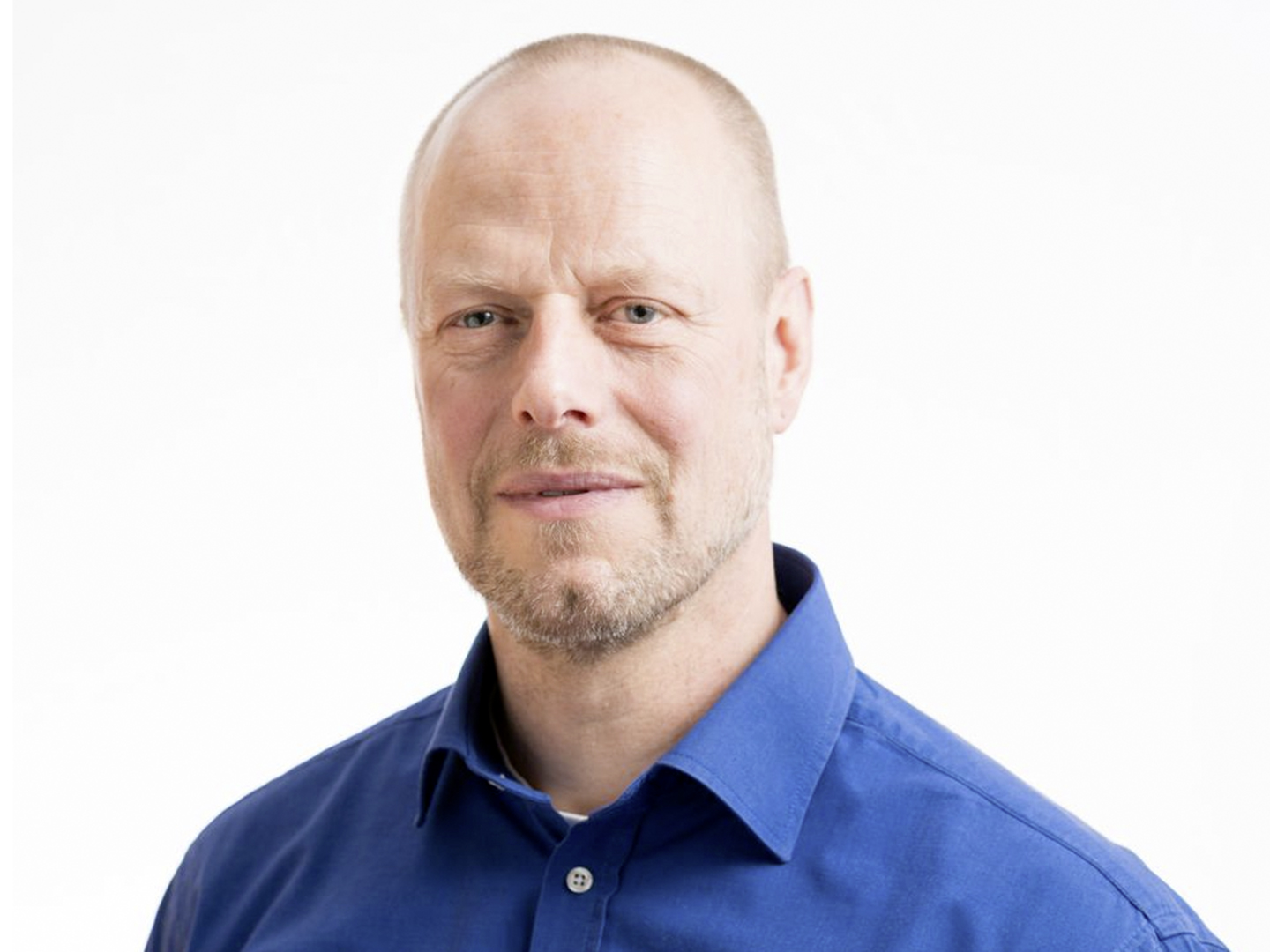
You are subproject lead for scientific work at your institute in the L-VIII subproject. What has been achieved so far in this area within the Carbon2Chem® research project?
Frank Atzler: This question actually has to be answered in a relatively large context as, taken alone, results from the world of powertrains are perhaps not particularly exciting, especially when talking about technologies perceived as “yesterday’s news”, not just by the public, but by many colleagues as well.
I’ll attempt a very concise summary: Electricity will be the future of our energy supply. In order to guarantee the supply of energy even when the wind is not blowing and the sun is not shining, electricity needs to be stored. Chemical storage is a very attractive choice as it allows for very high energy densities and a long “shelf-life”, for example throughout the whole year. This approach first leads to hydrogen as the basic substance for storage. However, in addition to a few other undesirable physical properties, it has a very low volumetric energy density. So we bind the hydrogen to recycled carbon molecules. We can do this really well with methanol on a large industrial scale at competitive prices. Methanol is just as suitable for stationary storage as it is for transport around the globe. The green MeOH can then be used at its destination for reconversion into electricity during blackouts, as a national or Europe-wide strategic energy reserve, as a raw material in the chemical industry, but also for future mobility, for example. And that’s where we come in.
We are the ones who deliver torque and speed to drive all kinds of applications, such as the reconversion that I just mentioned or the drive of a small, affordable CO2-neutral car. And with drives, you can make a very simple distinction: For stationary applications, e.g., combined heat and power plants, cements works or in steel manufacture, electricity and hydrogen can be provided via supply lines. Energy density and storability take a back seat. For mobile applications, it’s completely different. Here, ease of handling, refueling speed and the highest volumetric energy density possible for usable driving ranges all play a decisive role. Also, the energy store, i.e., the tank, should not be heavy or expensive. Methanol is the simplest and cheapest Carbon2Chem® fuel to produce on a large scale, and can easily be filled into a cheap, lightweight tank. It has only half the volumetric energy density of diesel fuel but twice as much as LIQUID hydrogen (-253 °C!!) and about 3 to 6 times as much as gaseous H2, based on 700 and 350 bar storage pressure.
What has been achieved to date: When it comes to developing an optimum combustion process for methanol, we have established that it is practically as efficient as a fuel cell, and that, compared to other drive units, we can achieve an extremely robust solution at an unparalleled price! If such a combustion engine is now paired with an electric machine in combination with a battery that is much smaller than that of a pure battery-powered vehicle to give a “super hybrid drive”, then the energy consumption for the load spectrum for which the drive had been designed can be reduced even further! So we have a robust, affordable solution with simple energy logistics and handling for mobile applications that is also CO2-neutral! Outlining this drive is our ambitious and exciting goal in the Carbon2Chem® project!
What have been the highlights?
Frank Atzler: Our task in Carbon2Chem® is to put such a “super hybrid” concept though its paces and to develop it further. Since the project is still in its early days, the highlights aren’t yet monumental. But despite the recent challenges caused by supply issues and Covid-19 restrictions, we have managed to build an entirely new test bench and I am very pleased with our progress in terms of time and technology. What makes it special is that we have mechanically decoupled the engine and the connected generator for our research and can now actually evaluate the system parts individually. This was not possible before and will help us considerably in optimizing the overall system.
What were the biggest challenges?
Frank Atzler: Actually, that was the supply difficulties, waiting for parts and materials. We are currently about six weeks behind schedule.
Decoupling the engine from the integrated system required a complex feat of engineering. We had to design and manufacture a number of special parts for that. But we can do that in house, and those are the sorts of challenges that an engineer thrives on.
What are the next steps?
Frank Atzler: Now we are looking forward to the first baseline measurements, to pinpoint what we can thermodynamically and mechanically target and improve. From our prior experience with methanol applications, we already know roughly what to expect and where to go from there. As always, the devil will be in the detail, but of course that is the very nature of research! And as I said, that is what researchers relish!