Carbon2Chem®
Making steel production climate-friendly
Making steel production climate-friendly – this is the goal Carbon2Chem® started with in March 2016. The first phase of the joint project funded by the Federal Ministry of Education and Research was completed in May 2020. During these four years, process concepts have been developed which help to capture and clean the CO2-containing exhaust gases from Germany's largest steel mill and convert them into basic materials for chemicals, fuels or fertilizers using “green” hydrogen. In the second project phase, these concepts will be validated for large-scale implementation.
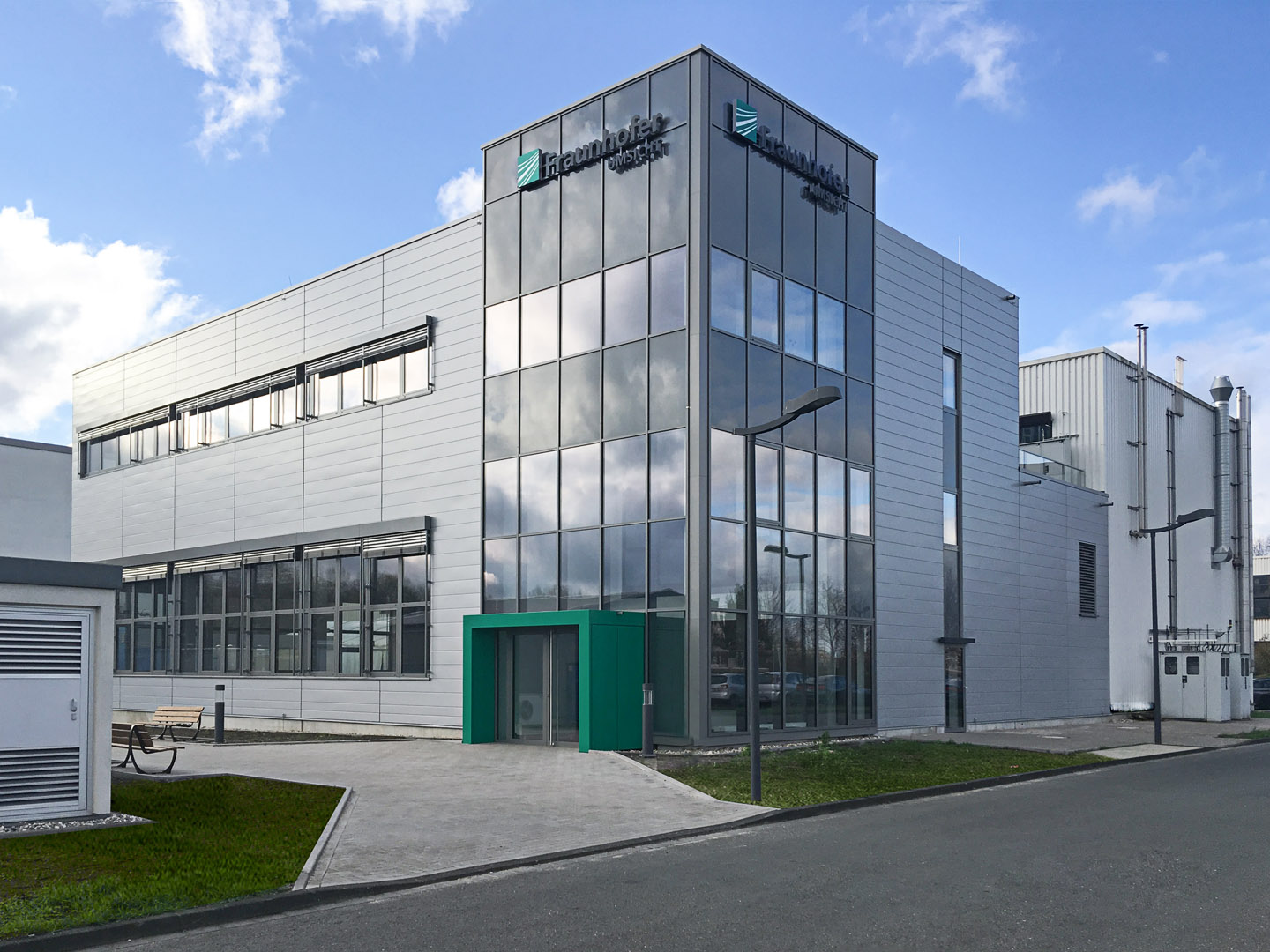
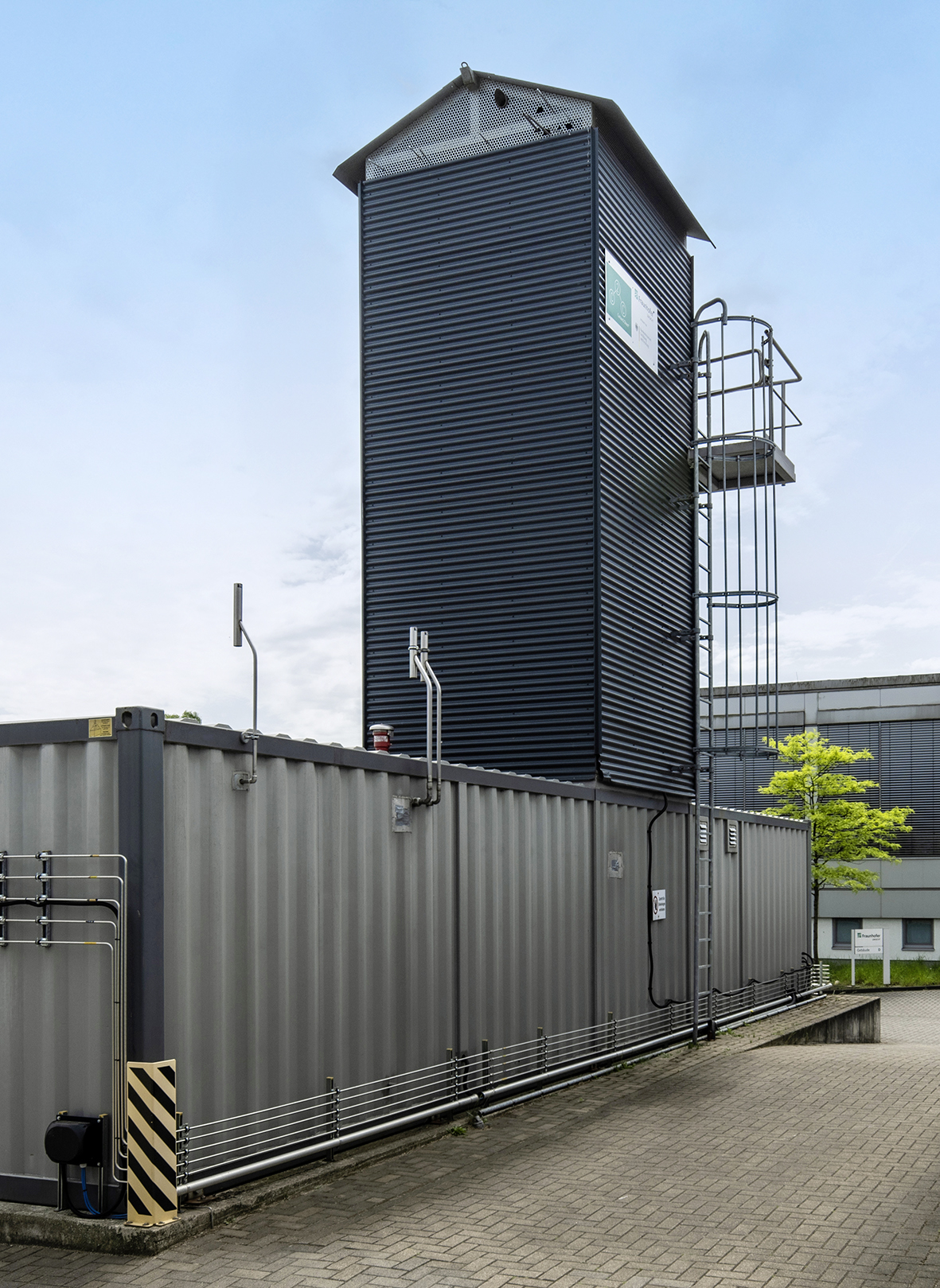
“The consortium of basic research, application-oriented research and development, and industry behind Carbon2Chem® has proven itself”, says office manager Dr.-Ing. Torsten Müller. “The partners work together in a committed and goal-oriented manner. Together they have achieved that the project is a flagship of national energy research.” A total of almost 20 companies and research institutions are involved. They are coordinated by the Max Planck Institute for Chemical Energy Conversion, the Fraunhofer Institute for Environmental, Safety, and Energy Technology UMSICHT and thyssenkrupp Carbon2Chem GmbH.
Carbon2Chem® infrastructure: Places of joint research and development
Research and development take place among other things in the joint technical center at the thyssenkrupp site in Duisburg. Opened in 2018, its proximity to the steel mill will provide direct access to real steel mill gases and the opportunity to conduct tests under industrial conditions. In addition, the Max Planck Institute for Chemical Energy Conversion and Fraunhofer UMSICHT operate the project laboratory in Oberhausen, which was inaugurated in early 2019. Here, joint research is being conducted on processes for gas purification and for the production of methanol and higher alcohols.
A further component of the Carbon2Chem® infrastructure will also go into operation in 2019: In the methanol pilot plant in Oberhausen, trials are underway to simulate the production of methanol from metallurgical gas in terms of process engineering. In the second project phase, the plant will move to the pilot plant in Duisburg, where it will produce up to 75 liters of raw methanol per day from the metallurgical gases.
Research results: From water electrolysis to gas purification and synthesis
Important detailed results have been achieved at these locations during the first funding phase. Among other things, it could be shown that the hydrogen recovered from steel mill exhaust gases can be used directly for chemical-catalytic processes after purification. A further finding: Alkaline electrolysis can also be operated dynamically – without aging effects or efficiency losses. In this context, dynamic operation means that the plant is controlled according to the supply of renewable electricity.
In the field of gas cleaning, new strategies could be developed and optimized. A corresponding plant was built and successfully operated. It relies on pressure swing adsorption, gas scrubbing and compression. Furthermore, experimental results are available for thermocatalytic and plasma catalytic oxygen removal (DeOxo process).
At the end of 2018, the pilot plant succeeded for the first time in producing methanol and ammonia on a laboratory scale from real metallurgical gas. In the second phase of the project, the aim is to show that these processes also function stably on a large scale and lay the foundations for low-emission operation of the steel mill in Duisburg. The BMBF is providing a further 75 million euros for this up to 2024.
Last modified: