… Dr. Barbara Zeidler-Fandrich and Sungyoun Suh from Fraunhofer UMSICHT
Interview of 15.09.2021
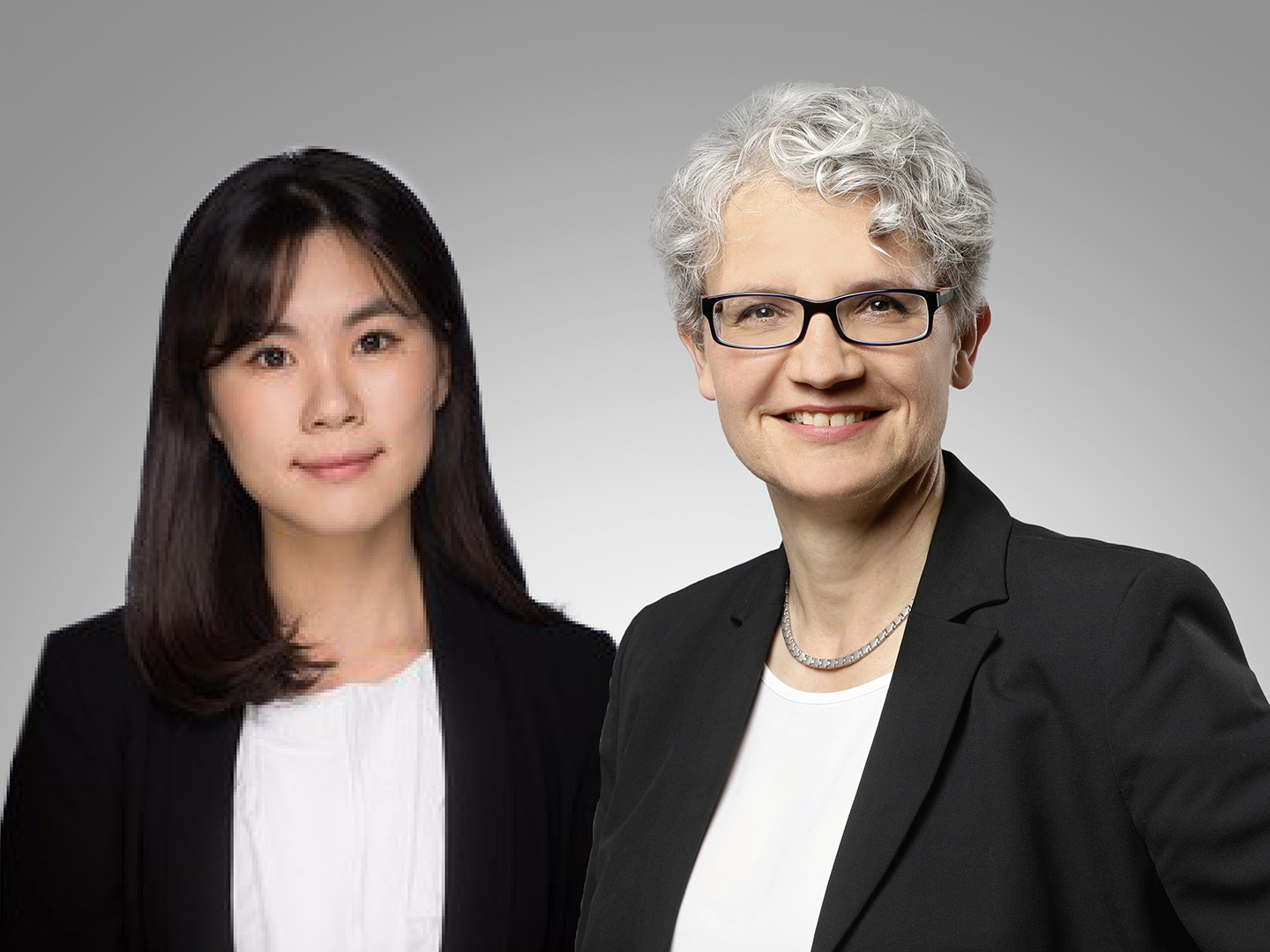
As scientists at Fraunhofer UMSICHT, you work in applied research and you are involved in the research project in the context of gas purification and use, specifically thermal catalysis. What has been achieved so far in this area within Carbon2Chem®?
Barbara Zeidler-Fandrich: As part of the Carbon2Chem® subproject, we are developing various processes for the treatment of coke oven gas. As well as the thermo- and plasma-catalytic removal of trace oxygen from the pressure swing adsorption feed gas stream, we have developed electric swing adsorption (ESA) to separate off high-boiling hydrocarbons. With this work, we are addressing issues for which there are currently no established processes.
A special test plant was therefore designed for each of the processes we investigated and built in the Carbon2Chem® laboratory in Oberhausen. In operation with synthetic coke oven gases, we were able to demonstrate the suitability in principle of all three gas treatment processes.
Sungyoun Suh: Our work in subproject L-III relates to the treatment of coke oven gas. Catalytic pre-purification is necessary to remove the trace oxygen for the subsequent pressure swing adsorption. In the first phase of Carbon2Chem®, three catalyst systems for purifying the synthetic coke oven gas were investigated and evaluated on a laboratory scale. The investigation showed that the traces of oxygen can be significantly reduced with all catalyst systems. In addition, investigations have been carried out into catalytic poisoning and regeneration processes in which H2S was considered to be a catalyst poison. It has been shown that a catalyst can be used in several cycles over the long term in the presence of catalyst poison. As well as the noble metal catalyst, non-noble metal catalysts also show promise.
What have been the highlights?
Barbara Zeidler-Fandrich: In each of the three processes investigated over the course of the project to date, we have had quite different highlights. For instance, in the case of plasma catalysis with non-thermal plasma, not only were we able to show that a targeted conversion of trace oxygen takes place, but we were also able to take the first steps toward scaling the process up. For this purpose, a scalable DBD test reactor with a steel shell was built and successfully used. In the electric swing adsorption, one of the main highlights was the modification of the electrode geometry which allowed us to adjust the fixed bed temperature in a targeted manner. And in the case of thermocatalytic oxygen removal, we were able to demonstrate that the non-noble metal catalysts we tested are also suitable in principle for removing oxygen from coke oven gases. This paves the way for developing a cost-effective process using inexpensive catalyst materials.
Sungyoun Suh: One of our successes was in the context of testing the non-noble metal catalysts that have not previously been considered for oxygen removal. These catalyst materials have been around for decades and are already used successfully in other industry processes. Nevertheless, new applications for these commercial materials are always being discovered. Compared to the noble metal catalyst, they are cheaper and even consume sulfidic components.
What were the biggest challenges?
Barbara Zeidler-Fandrich: The greatest challenges were working in parallel on developing three new processes and the uncertainties regarding the trace gas components present in the coke oven gas. Although articles have been published on this topic, they do not generally cover everything. The work of the Max-Planck Institute for Chemical Energy Conversion now provides some pointers, but this was not available when the test plants were being designed.
Sungyoun Suh: The biggest challenges were to understand the reaction mechanisms on the catalyst surface and to work out the optimum test conditions for oxygen removal. We use complex spectroscopic methods to identify the active sulfidic centers.
The aim is to work out the correlation between the formation of the active species and the catalytic activity in terms of oxygen removal. Technical problems crop up from time to time and we come up against the technical limits of our test plants. Maintaining the balance between technical feasibility and theoretical ideas is not easy.
What are the next steps?
Barbara Zeidler-Fandrich: Now that the suitability in principle of all three processes has been demonstrated on a laboratory scale using synthetic coke oven gases, we intend to extend the gas matrix to selected trace and secondary gas components. We will also look at specific issues such as the influence of the process pressure or fluctuating gas streams. We anticipate important findings for further process development. At the same time, a scale-up to pilot plant scale and operation with real gases will take place at the Duisburg Carbon2Chem® technical center.
Sungyoun Suh: In the second phase of the project, we will carry out the tests not just in the lab but also using real gases in the Duisburg technical center. The process will be scaled up accordingly and assessed for use under real conditions.
For the use of the non-noble metal catalysts, further lab experiments are needed to understand the complex chemical reactions and to then optimize the process. To do this, in tandem with the tests at the Duisburg site, we will systematically extend the gas matrix of the synthetic coke oven gas in the Oberhausen lab by adding other catalyst poisons such as COS or aromatic components.