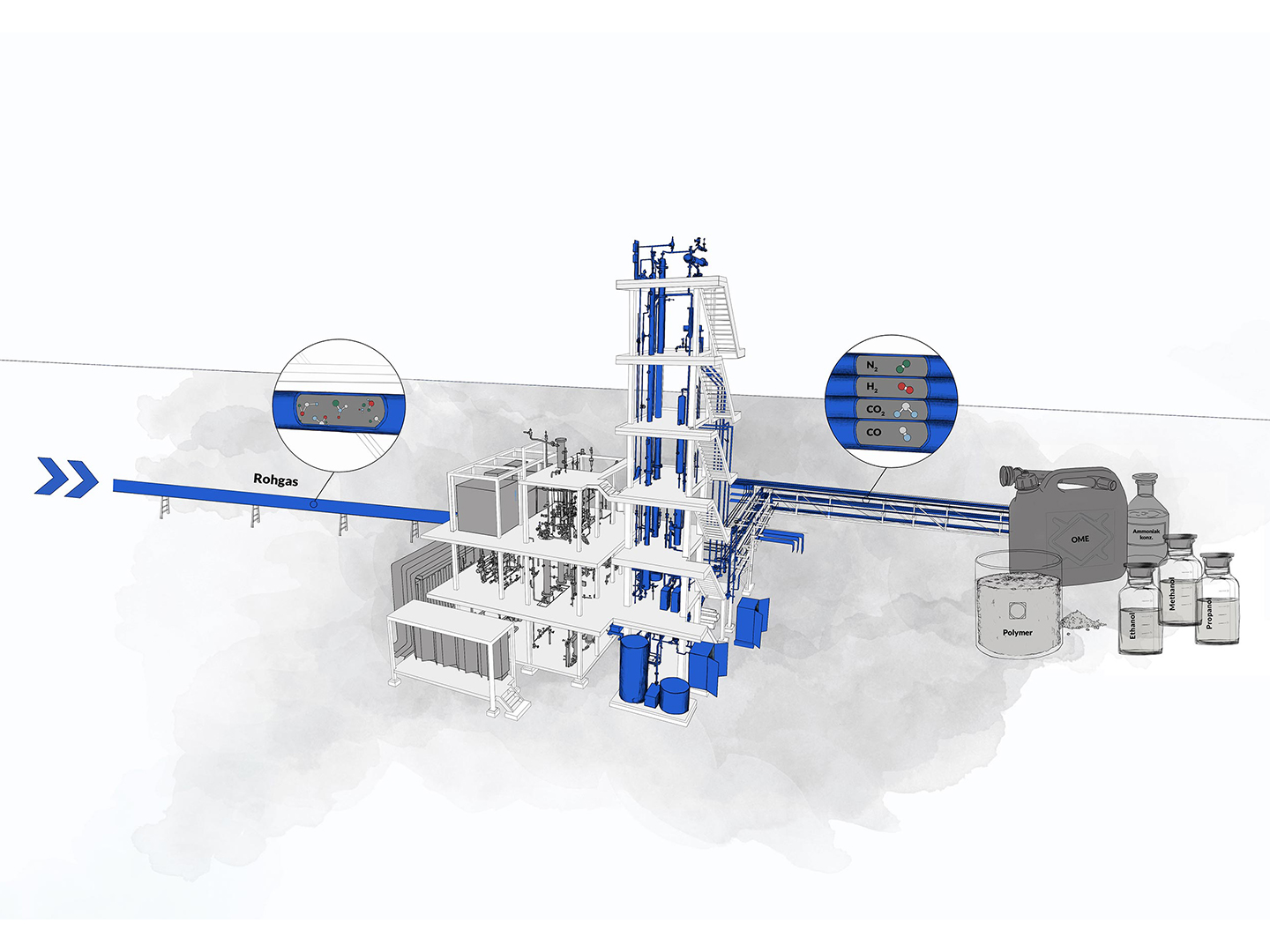
Each synthesis requires a corresponding gas quality: The different gas utilization options of Carbon2Chem® require an adapted cleaning process chain for the raw gases. The process steps are adapted, tested, and optimized on a pilot scale using real gas in the technical center. Innovative process approaches are investigated on a laboratory scale with regard to their feasibility.
In addition to gas purification, the subproject also deals with the laboratory validation of ammonia synthesis on the basis of metallurgical gases. |
Tasks
Subproject L3 researches the processing of converter, blast furnace, and coke oven gas. The focus lies on the provision of a syngas in the highest possible quality for chemical production. Catalytic pre-purification and a subsequent fine cleaning by means of pressure swing adsorption are the key steps in the recovery of pure hydrogen from coke oven gas. Catalytic pretreatment and amine scrubbing are used to extract high-purity CO and CO2 from converter gas. The gas treatment plant is shown and developed on a scale of 100 Nm³/h in a technical center, which is connected to the pipeline network of the Duisburg-Schwelgern network site. Innovative process steps are flanked by laboratory tests on a scale of 1 Nm³/h.
Aims
The main objective of the L3 project is to develop the economically and technologically optimal purification process for metallurgical gases in order to present syngases in the required purities. The work in the technical center serves to verify a commercially feasible basic concept. The laboratory work also allows for process intensification as well as greater flexibility in gas composition, as expected at other metallurgical sites. The modeling of these process steps and a data export to subproject L0 are absolutely necessary to develop the overall concept, including further synthesis steps, and to evaluate them in detail.