Auszeichnung
Innovationspreis für Klima und Umwelt geht an Fraunhofer UMSICHT und Volterion
Für ihr gemeinsames Projekt »Kostengünstige stationäre, skalierbare Redox-Flow-Batterien und deren Produktionsprozess« haben Forschende des Fraunhofer UMSICHT und der Volterion GmbH & Co. KG den Innovationspreis für Klima und Umwelt (IKU) in der Kategorie »Produkt- und Dienstleistungsinnovationen für den Klimaschutz« erhalten. 2022 erstmals vom Bundesministerium für Wirtschaft und Klimaschutz verliehen geht die Auszeichnung an Unternehmen und Einrichtungen, deren Ideen neue Wege im Bereich Klima- und Umweltschutz aufzeigen. UMSICHT und Volterion konnten die Jury vor allem durch die umwelttechnischen Vorteile der von ihnen entwickelten Redox-Flow-Batterien überzeugen.

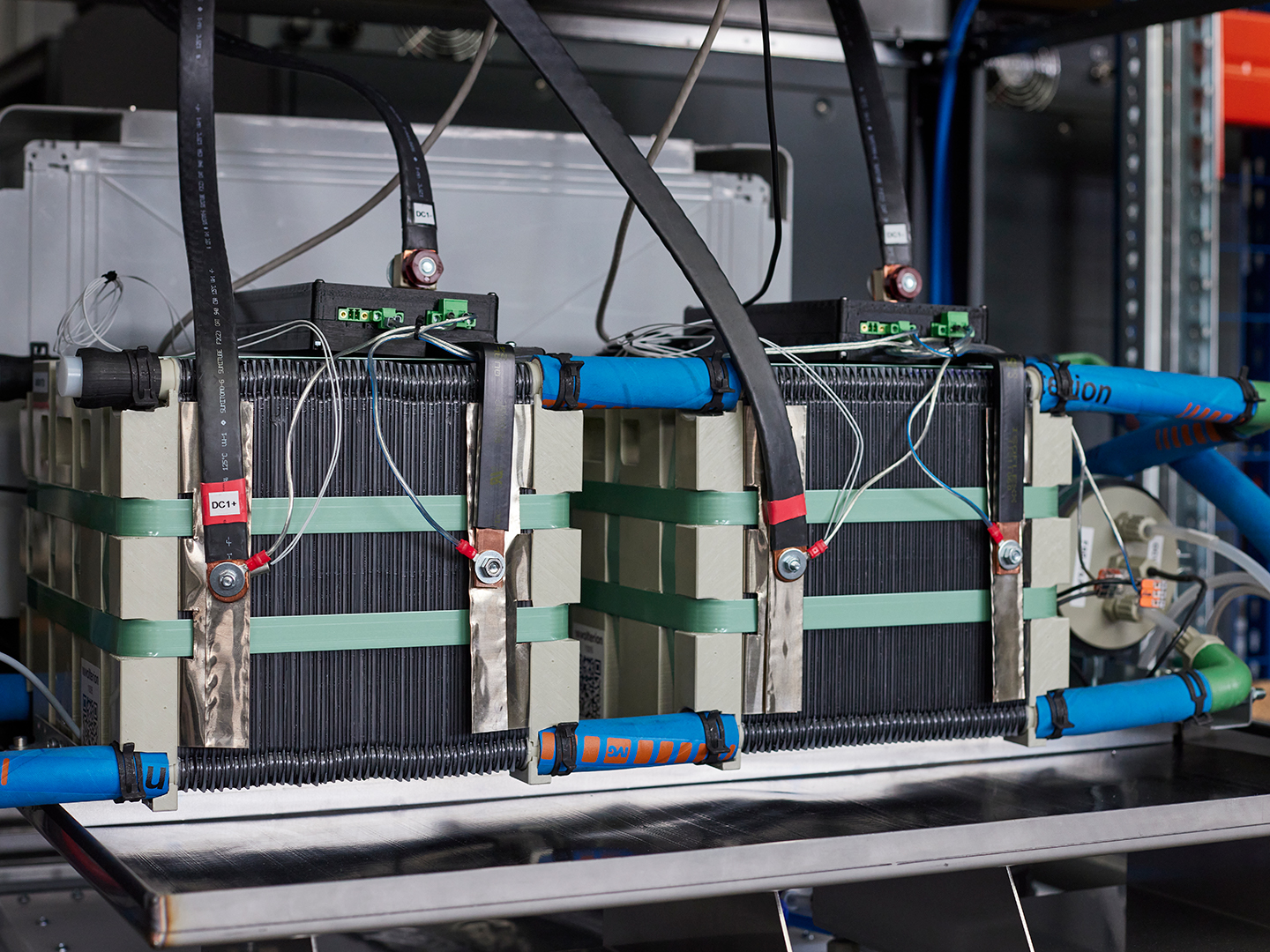
Im Gegensatz zu Lithium-Ionen-Batterien, die u.a. auf kritischen Materialen wie Kobalt basieren und auch äußert schwierig zu recyceln sind, werden bei der Produktion von Redox-Flow-Batterien Mensch und Umwelt geschont. Diese Energiespeicher lassen sich auch für sehr große Energiemengen auslegen und werden dabei spezifisch kostengünstiger. Im Betrieb wird der flüssige Elektrolyt aus Vanadium regelmäßig regeneriert und kann außerdem nach 20 und mehr Jahren stofflich recycelt werden. Das enthaltene Vanadium kann zu neuem Elektrolyt werden. Zudem sind die Batterien nicht brennbar und zyklenstabil. Ihre Kapazität nimmt also auch nach tausenden Lade-/Entladezyklen nicht merklich ab.
Redox-Flow-Batterien tauglich für den Massenmarkt machen
Im Fokus der Forschenden stand die Frage, wie sich diese Batterien – die sich hervorragend für die stationäre Speicherung fluktuierender Energien aus Windkraft- und Solaranlagen eignen – kostengünstiger herstellen lassen. Denn: Das Herz einer Redox-Flow-Batterie – der sogenannte Stack – besteht üblicherweise aus über 150 gestapelten Komponenten (Bioplarplatten, Graphitfilzen, Membranen, Stromleiterplatten, Gehäuse usw.), die mit einer Vielzahl von Schrauben und massiven Metallplatten zusammengehalten und mit zahlreichen Dichtungen abgedichtet werden. Die Kosten für Material und Aufbau sind entsprechend hoch. Prof. Dr. Christian Doetsch, Dr. Anna Grevé, Lukas Kopietz und Peter Schwerdt vom Fraunhofer UMSICHT sowie Dr. Thorsten Seipp und Sascha Berthold von Volterion haben deshalb ein neues, vollverschweißtes Stackkonzept erarbeitet – und zwar auf Basis einer selbstentwickelten, verschweißbaren Kunststoff-Bipolarplatte.
Als Ausgangsstoffe für die Bipolarplatte wählten die Wissenschaftlerinnen und Wissenschaftler die üblichen Grafite und Ruße, gingen aber auf andere Art und Weise an den Herstellungsprozess heran: Kunststoffpellets werden zunächst bei bis zu minus 80°C zu Pulver zermahlen und mit der vierfachen Menge Graphit gemischt. Diese Pulvermischung schicken sie durch ein System aus mehreren Walzen mit unterschiedlichen Temperaturen und Geschwindigkeiten. Zwischen den Walzen wird das Pulver bei moderaten Temperaturen und geringen Drücken aufgeschmolzen, intensiv geknetet, zu einer Bahn gewalzt und schließlich aufgewickelt.
Das neue Material erhält dabei thermoplastische Eigenschaften, ist also biegsam und verschweißbar, trotz des relativ geringen Kunststoffanteils. Der Stack kommt somit ohne eine einzige Dichtung aus, auch Schrauben sind überflüssig – die Zellen werden einfach in einem automatisierten Verfahren miteinander verschweißt. Das hat erhebliche Vorteile für die Redox-Flow-Batterien: Der entwickelte Stack ist von den Materialkosten her 40 Prozent günstiger als ein herkömmlicher Stack, auch die Produktionskosten konnten deutlich gesenkt werden. Zudem wiegt er 80 Prozent weniger und ist nur etwa halb so groß.
Produktion via Pulver-zu-Rolle-Verfahren
Der zweite entscheidende, weil kostensenkende Schritt war die Entwicklung des kontinuierlichen Produktionsverfahrens: das Pulver-zu-Rolle-Verfahren, in dem sich die Bipolarplatten als Endlos-Bahn auf Rolle fertigen lassen. Auf diese Weise lassen sich sehr dünne Platten herstellen, bis hinab zu 0,1 Millimetern. Es ist also deutlich weniger Material notwendig, was den Preis wiederum senkt sowie leichtere und kompaktere Stacks ermöglicht. All dies schafft ganz neue Möglichkeiten in der Konstruktion, die in der Volterion GmbH & Co. KG bis hin zur ganzen Batterie umgesetzt werden.
Letzte Änderung: