Schlüssel der Energiewende: Leistungsstarke Redox-Flow-Batterien
Newsletter 7.03.2018 - Da Wind- und Sonnenenergie fluktuieren, besteht eine große Herausforderung der Energiewende darin, den Stromfluss zu verstetigen. Dies können elektrische Energiespeicher leisten. Auf der ENERGY STORAGE präsentiert Fraunhofer UMSICHT vom 13. bis 15. März 2018 in Düsseldorf (Stand B39, Halle 8b) besonders langlebige Redox-Flow-Batterie-Stacks und hochflexible Bipolarplatten, mit denen Einzelzellen zu leistungsstarken Stacks verbunden werden. Die Newsletter-Redaktion sprach mit Lukas Kopietz und Jan Girschik über die vielversprechende Technologie und weitere neue Entwicklungen.
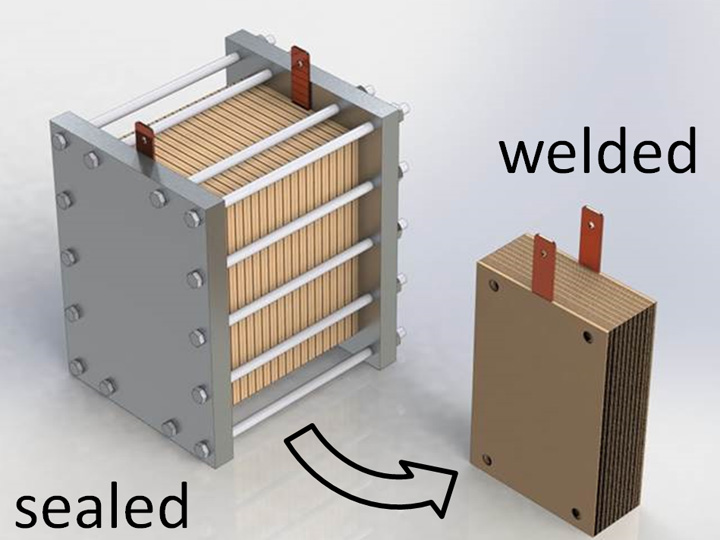

Für welche konkreten Anwendungen ist der Redox-Flow-Stack - der auf der Messe aufgestellt wird - interessant?
Jan Girschik: Redox-Flow-Batterien eignen sich prinzipiell vor allem als stationäre Energiespeicher und wurden mit diesem Ziel auch in den 70ern von der NASA entwickelt. Das liegt zum einen an den relativ geringen Energiedichten der Elektrolytlösungen, in denen die Energie chemisch gespeichert wird, zum anderen aber auch an Eigenschaften wie der Tiefentladefestigkeit und der nahezu nicht vorhandenen Selbstentladung, die eine mittel- und langfristige Speicherung großer Energiemengen erst effizient machen. Der größte Vorteil von Redox-Flow-Batterien ist jedoch die Möglichkeit der unabhängigen Skalierbarkeit von Leistung und Kapazität.
Somit kann ich das Batteriesystem optimal auf den Anwendungszweck auslegen, solange es sich dabei um eine ortsfeste Installation handelt. Die Möglichkeiten reichen dabei vom Einsatz in Privathaushalten, zur Eigenstromnutzung der Photovoltaikanlage auf dem Dach bis hin zur Sicherung der Netzstabilität mit Massenspeichern, um Leistungsschwankungen durch die Volatilität erneuerbarer Energien abzufangen und eine unterbrechungsfreie Stromversorgung garantieren zu können.
Die Dimensionen der Redox-Flow-Batterien variieren dabei entsprechend den Anforderungen. In Privathaushalten kann man zum Beispiel einen Speicher der Volterion GmbH mit einer Leistung von 4kW und einer Kapazität von 10kWh einsetzen, während der Energieversorger EWE gerade den Einsatz einer Redox-Flow-Batterie mit 120MW Leistung und 700MWh Kapazität plant. Die Besonderheiten des Prototypen-Stacks, den wir auf der Messe zeigen, sind zum einen, dass die einzelnen Zellen stoffschlüssig zu einem Batteriestack zusammengeschweißt und damit absolut flüssigkeits- und gasdicht sind. Zum anderen weist der Batteriestack sehr geringe zellinterne Druckverluste und eine entsprechend geringere Materialbeanspruchung gegenüber anderen Zelldesigns auf. Beides wichtige Faktoren, um den Ruf der Redox-Flow-Batterie als Energiespeicher mit einer besonders hohen Zyklenfestigkeit und Lebensdauer von bis zu 20 Jahren aufrechtzuerhalten und weiter auszubauen. Als Anwendungen sehe ich daher stationäre Speicheraufgaben, die eine besonders langlebige, umweltsichere und wartungsarme Speichertechnologie erfordern.
Wie sehen die Marktchancen prinzipiell für beide Entwicklungen (Exponate) aus?
Jan Girschik: Mit der erfreulichen Zunahme des Anteils erneuerbarer Energie an der Stromerzeugung steigt zum Lastausgleich natürlich auch der Bedarf an zuverlässigen und effizienten Energiespeichern. Und mit den Etappenzielen des Bundesministeriums für Wirtschaft und Energie, den Anteil der Erneuerbaren Energien am deutschen Bruttostromverbrauch bis 2020 auf 35% und bis 2030 auf 50% zu steigern, sehe ich vor allem einen Markt für Speicher mit großen Leistungen und Kapazitäten. Die Leistung einer Redox-Flow-Batterie kann dabei entweder durch die Serienschaltung mehrerer Zellen zu einem Stack oder durch den Einsatz von Zellen mit größeren aktiven Flächen gesteigert werden.
Der Prototypen-Stack, den wir auf der Messe zeigen, besteht aus fünf Einzelzellen mit aktiven Flächen von je 1100cm², die zusammen eine Nennleistung von 450W erzeugen. Um die gleiche Leistung zu erzeugen, könnte ich aber auch nur eine Batteriezelle mit einer aktiven Fläche von 5500cm² nehmen. Diese würde theoretisch günstiger in der Fertigung sein, da der Bearbeitungsaufwand proportional zum Umfang der Zelle ist. In unserer Batterie-Gruppe bei UMSICHT haben wir uns deshalb das Ziel gesetzt, die aktive Zellfläche sukzessive in den Quadratmeterbereich zu steigern. So einfach, wie es klingt, ist es aber leider nicht, da mit der Vergrößerung der Zellfläche zum Beispiel auch die systemimmanenten Druckverluste steigen, die gleichmäßige Eduktverteilung wird schwieriger, und außerdem fehlte bis vor kurzem noch die Möglichkeit eine Kernkomponente unserer vollverschweißten Redox-Flow-Batterie entsprechend großformatig herstellen zu können: die Thermoplast basierte Bipolarplatte, mit der aus Einzelzellen ein Batteriestack wird.
Lukas Kopietz: Vor allem in Redox-Flow-Batterien können wir einige Vorteile der Bipolarplatte nutzen wie zum Beispiel die geringe Materialstärke und gute Verschweißbarkeit. In unserem ausgegründeten Unternehmen Volterion GmbH sind diese Platten bereits im Einsatz. Die graphitbasierte und kunststoffgebundene Bipolarplatte verbindet jedoch nicht nur in Redox-Flow-Batterien mehrere Zellen vollflächig miteinander, sondern ebenfalls in Polymer-Elektrolyt-Membran-Brennstoffzellen. Speziell jetzt, wo die fossilen Energieträger für negative Schlagzeilen sorgen, wird der Einsatz von Brennstoffzellen wieder interessant. In dieser Anwendung macht die Bipolarplatte rund 40% bis 60% der Systemkosten aus. Diese können wir mit unserem Verfahren und unseren Materialien deutlich senken. Außerdem erhoffen wir uns, die Bipolarplatten in Zukunft auch für mobile Anwendungen etablieren zu können.
Welche nächsten Ziele verfolgen Sie bei Ihrem Projekt?
Lukas Kopietz: Mit unserer neuen Anlage zur kontinuierlichen Herstellung der Bipolarplatten erschließen sich ganz neue Möglichkeiten der Fertigung. Für den Einsatz in Flow-Batterien plane ich, die Materialdicke sukzessive zu verringern. Dies bringt nicht nur eine Kosten- und Gewichtsersparnis, sondern kommt auch unserem Herstellungsprozess zugute.
Neben dem Einsatz der Bipolarplatten in der Batterie- und Brennstoffzellentechnik, möchte ich die Materialien auch für gänzlich andere Anwendungen etablieren. Durch Variation der Rohmaterialien und der Füllgrade können unterschiedliche Eigenschaften eingestellt und realisiert werden. Hierzu habe ich unter anderem erste erfolgreiche Versuche unternommen, vollflächige Heizelemente herzustellen. Ziel wäre es, sogenannte »wearables« herzustellen, also Fasern oder flächige, flexible Stücke, die die Beheizung von Kleidung ermöglichen. Auch einen anschließenden Einsatz als flexible Begleitheizung haben wir diskutiert. Bei einem hohen Anteil an Graphit eignen sich die Werkstoffe zudem als selbstschmierende Lager, eine Abschlussarbeit ist zu dem Thema vor einiger Zeit fertiggestellt worden.
Jan Girschik: Bei mir dreht sich vorerst alles um die Realisierung großformatiger Redox-Flow-Batterien. Aufgrund der Komplexität des diametralen Verhaltens von elektrischen und hydraulischen Widerständen innerhalb der Batteriezellen handelt es sich dabei nicht mehr um ein einfaches Scale-up, sondern vielmehr um eine Weiterentwicklung. Aktuell tüftle ich an einer Zelle mit einer aktiven Fläche von 4000cm², die sich bereits in der Simulation bewährt hat und zumindest in der Theorie Druckverluste von gerade einmal 400mbar aufweist. Gegenüber einem konventionellen Zelldesign entspricht das einer Reduzierung der hydraulischen Widerstände um Faktor 10. Das nächste Ziel ist es also, diese Batteriezelle zu fertigen und erfolgreich zu testen.
Welche besonderen Herausforderungen gab es bei der Herstellung der Bipolarplatte?
Lukas Kopietz: Wir haben uns bei der Materialauswahl an damaligen Forschungsarbeiten orientiert. Leider waren die Werkstoffe für unsere Anwendung so nicht brauchbar, speziell die mechanische Stabilität war ein großes Problem. In Abstimmung mit unserer Batterie-Gruppe haben wir nach und nach flexible Materialien eingesetzt und diese kontinuierlich optimiert. In unserer Arbeitsgruppe verfolgen wir die Herstellung dichtungsfreier, also vollverschweißter Batterien. Die Verschweißbarkeit der Materialien einzustellen, war eine große Herausforderung. Außerdem ergibt sich mit jedem neuen Grundmaterial eine neues Werkstoff- und Prozessverhalten, so dass ich oftmals bei Null anfangen musste.
Großformatige Bipolarplatten können auch für PEM-Brennstoffzellen hergestellt werden: Ist dies auch eines Ihrer nächsten Ziele?
Lukas Kopietz: Interessant für die Brennstoffzelle wird speziell der Aspekt der kontinuierlichen Fertigung, hierdurch können wir die Materialien sehr kostengünstig und in großen Mengen bereitstellen. Pro Brennstoffzellen-Stack werden rund 60 bis 100 Bipolarplatten benötigt. Für den Einsatz in mobilen Anwendungen wird das eine spannende Aufgabe.
Herausfordernd wird zudem die Materialauswahl. Die PEM-Brennstoffzelle arbeitet in einem Temperaturbereich zwischen 80°C (Niedertemperatur-PEM-BZ) und 220°C (Hochtemperatur-PEM-BZ). Hierfür müssen thermisch beständige Werkstoffe erprobt werden. Ferner übernimmt die Bipolarplatte in einer Brennstoffzelle die Zuführung und Verteilung (Sauerstoff und Wasserstoff) sowie Abfuhr der Medien (Wasser), wodurch sie mit einer Verteilerstruktur, einem sogenannten Flow-Field, versehen wird. Hierzu muss die Bipolarplatte nach der Herstellung nochmals umgeformt werden. Erste erfolgreiche Versuche habe ich durchgeführt, die Erkenntnisse müssen nun in den kontinuierlichen Prozess übertragen werden.